
LOGISTICS



Processing of composites by cutting
Our qualified specialists are ready to make custom spare parts for domestic and imported equipment. Modern polymer antifriction materials are used for production.
We offer the manufacture of polymer parts. Due to their flexibility and the ability to take different shapes, they are excellent for the manufacture of many parts that are used both in the sector of industry and in the household.
Efficiently and on time
The use of automated machining centers guarantees an improvement in the quality and accuracy of machining parts, minimizing the loss because of defects. Thanks to modern machines, the processing of composites becomes carefree: labor intensity is reduced, time for reconfiguration and readjustment of equipment is significantly saved, the influence of the human factor is reduced.
Our qualified specialists are ready to make custom parts from polymer materials for domestic and imported equipment:
-
Conveyor rollers.
-
Bushings and plain bearings for any equipment.
-
Slide guides (for chains and belts).
-
Sliding plates (shoes, slides, guides) for arrows and slide-out mechanisms.
-
Gears.
-
Wheels, pulleys.
-
Seals, gaskets, washers.
-
Non-standard parts and fasteners.
-
The cost of manufacturing parts is negotiable and depends on the selected material and the number of products.
-
Production time from 1 to 20 days.
-
The minimum batch is not limited.



Processing tolerance for parts manufactured by cutting
Such features of polymers as thermal expansion 10 times greater than that of metals, lower stiffness, moisture absorption ability, anisotropy, stress relaxation, subsequent shrinkage, lead to wider tolerances in the manufacture of products from them. A number of tolerances with a quality from 9 to 12 are usually applied. Tolerances with a quality of 7 and 8 are applied in special cases.
You will find more information in our Plastmass Group catalog. Please contact us to access our database.
Processing
of composites
Due to the high coefficients of thermal expansion, it makes sense to carry out size control only when room temperature is reached. The permissible size deviations of polymer parts are higher than those of metal parts.
Strain
To eliminate the formation of cracks, any mechanical treatment should be carried out at temperatures not lower than +18÷25°C.
Equipment
When processing ZEDEX materials, there are no high efforts of cutting. Therefore, for processing products made of ZEDEX materials, machines with lower capacities are sufficient than for processing the same metal products.
Tools
For the production of a large number of products, the use of tools made of HM (hardalloyed steel) is recommended. Serial production of parts with small tolerances requires the use of diamond-coated tools.
Sharpening
When turning ZEDEX materials, a high delivery is required. To obtain a high-quality surface, it is better to work with a wide cutter. The contour of the part and the surface must be done at a time.
Cooling
The best heat sink is the chip of the workpiece. Additionally, it can be cooled by a pressurized air jet, which would simultaneously clean the processing area from chips.
Sawing
When sawing with a strap saw, the speed of the strap should be between 8 and 25 m/sec. Blades and disks should have a sufficiently large tooth set with a tooth pitch from 4 to 6 mm.
Milling
To avoid overheating of the workpiece during milling, you need to choose the largest chip cross-section. This is achieved by a high delivery, large depth and cutting speed.
Reaming work
High accuracy of the hole dimensions is achieved by means of sweeps according to DIN 206, DIN 212, DIN 219. When choosing a sweep, it is necessary to take into account the elasticity of polymer materials and take a sweep with a diameter of at least 0.2 mm larger than the hole.
Screw cutting
The holes for thread sizes up to M8 should be approximately > 0.1mm larger than the holes for thread in metal, and the holes for thread sizes from M10 should be approximately > 0.2 mm.
Grinding
Almost all ZEDEX materials can be grinded and polished. Standard grinding belts and coarse-grained disks are used for grinding.
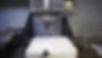